Last Updated on March 7, 2025

Introduction
The evolution of Programmable Logic Controllers (PLCs) has revolutionized industrial automation, transitioning from mechanical relay-based control to AI-driven intelligent systems. Over the decades, PLCs have become the backbone of manufacturing, enabling efficient, scalable, and automated operations. With advancements in AI in PLCs, IoT integration, and cloud-based automation, modern industrial control systems are smarter than ever. This article explores the journey of PLCs, from their early days to the future of machine learning in manufacturing.
The evolution of Programmable Logic Controllers is essential for industries looking to modernize and improve efficiency. Understanding these advancements helps manufacturers optimize production processes, enhance safety, and embrace the future of smart automation.
Early Days of Relay Logic in the Evolution of PLCs
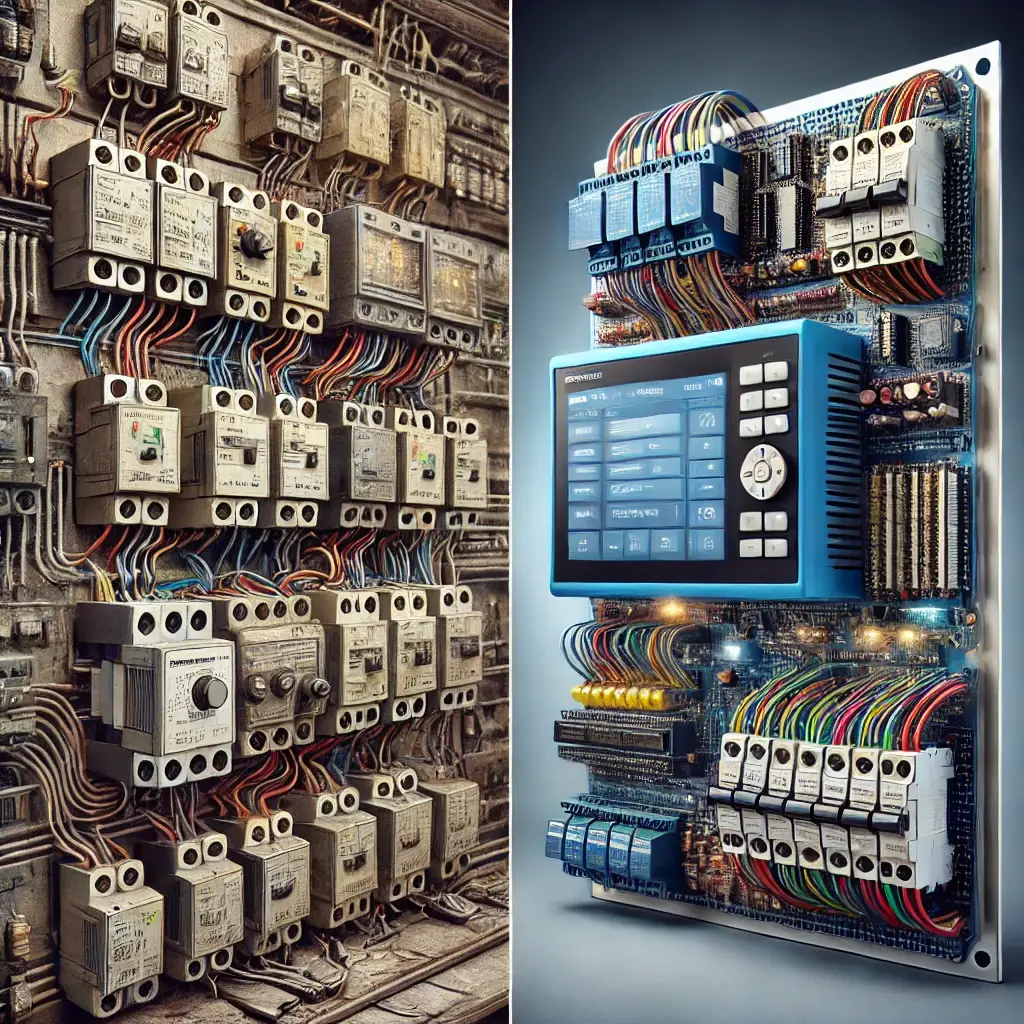
Before PLCs, industrial automation relied heavily on relay logicβa network of electromechanical relays that controlled circuits by physically opening and closing switches. While relay-based systems provided basic automation, they came with several drawbacks:
- βοΈ Bulky and complex wiring: Managing large-scale automation required extensive wiring, increasing the risk of errors and maintenance costs.
- β Limited flexibility: Changing control logic meant physically rewiring relays, leading to downtime.
- π§ High wear and tear: Mechanical relays suffered from frequent failures due to moving parts.
As industries sought more efficient and reliable control systems, the limitations of relay logic set the stage for the birth of Programmable Logic Controllers.
Birth of the PLC: A Milestone in the Evolution of Programmable Logic Controllers
The first commercially successful PLC was introduced in 1969 by Modicon (now part of Schneider Electric). Developed to replace cumbersome relay systems in the automotive industry, the PLC offered:
- π Electronic programming instead of mechanical wiring
- β‘ Faster response times and reduced maintenance
- π Reusability across different automation setups
Early adopters included automotive, chemical, and food processing industries, where flexible automation became critical for efficiency.
Key Advancements in the Evolution of Programmable Logic Controllers
As computing technology evolved, so did PLCs. Here are 10 game-changing advancements that shaped PLC programming and industrial automation:
1. π’ Microprocessors Revolutionizing PLCs (1980s)
The integration of microprocessors significantly improved the performance and capabilities of PLCs. Features introduced during this era included:
- π Ladder logic programming, making it easier for engineers to transition from relay logic.
- π Increased memory capacity, allowing more complex automation sequences.
- π Basic networking capabilities, enabling communication between multiple PLCs.
- β‘ Faster processing speeds, improving control response times.
2. π₯οΈ SCADA Systems and Connectivity (1990s)
The 1990s saw the rise of SCADA systems (Supervisory Control and Data Acquisition), allowing real-time monitoring and control of industrial processes. Key advancements included:
- π Distributed control systems (DCS) for large-scale automation.
- π οΈ Integration with sensors and human-machine interfaces (HMIs).
- π‘ Standardized industrial communication protocols like Modbus, Profibus, and Ethernet/IP.
- π Remote access to control systems, improving maintenance efficiency.
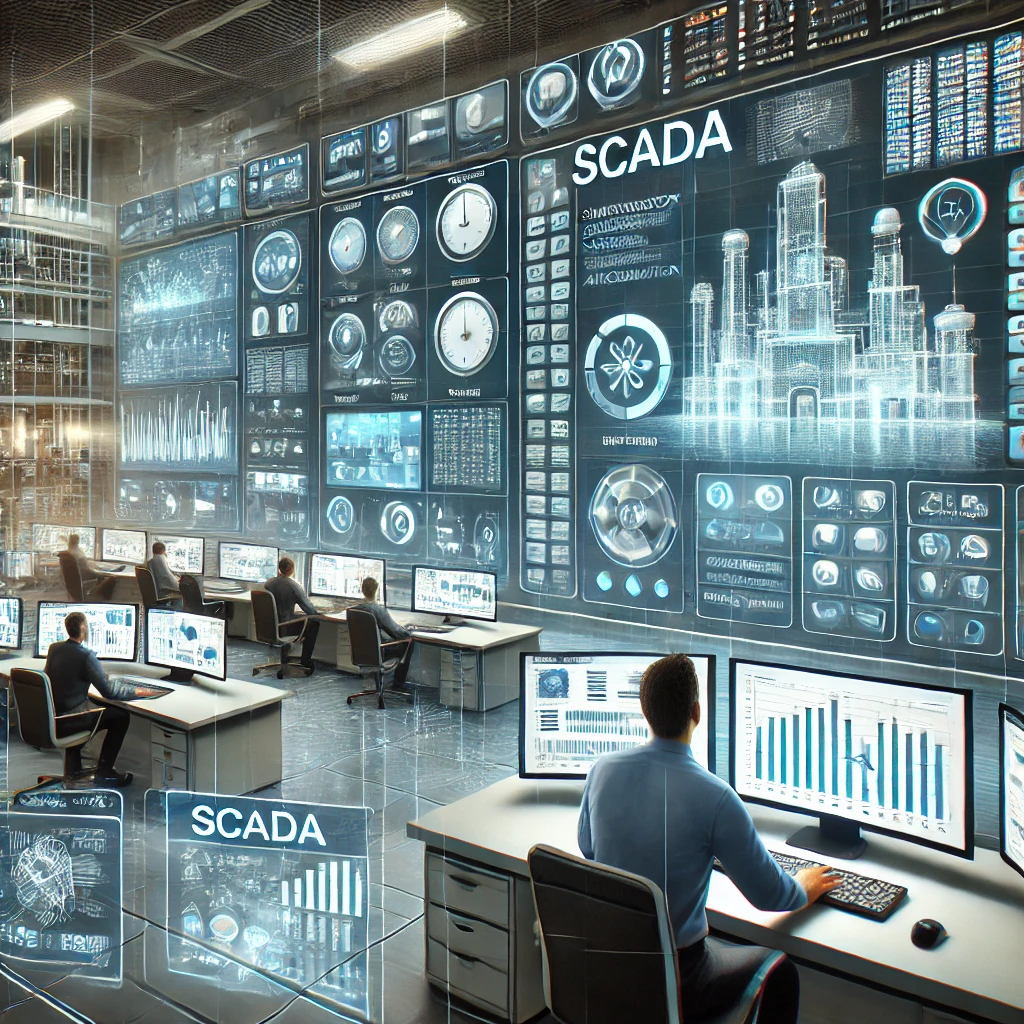
3. π Industry 4.0 and IoT Integration in PLCs (2000s)
With the onset of Industry 4.0, PLCs began evolving into connected, IoT-enabled automation controllers. Notable trends included:
- βοΈ Cloud-based automation, allowing remote access and monitoring.
- π Predictive maintenance, reducing downtime with real-time analytics.
- π Increased cybersecurity measures to protect connected systems.
- π Integration of big data analytics, enabling process optimization.
4. π€ AI and Machine Learning in the Evolution of PLCs
Today, AI-powered PLCs are enhancing manufacturing efficiency with intelligent decision-making capabilities. By incorporating machine learning in manufacturing, modern PLCs can:
- β οΈ Predict equipment failures before they occur, reducing unplanned downtime.
- π Optimize production processes by analyzing real-time data.
- π Automate complex tasks that traditionally required human intervention.
- π Adjust parameters dynamically, ensuring consistent output.
5. π₯ AI-Driven Quality Control with PLCs
Imagine a PLC-controlled production line equipped with AI-powered cameras, such as those used in modern automotive manufacturing. For instance, Teslaβs Gigafactories utilize AI-enhanced vision systems to inspect components in real time, ensuring high precision and quality in battery and vehicle assembly. These AI-driven cameras can detect microscopic defects, automatically adjust production parameters, and eliminate costly rework, improving efficiency and reducing waste.
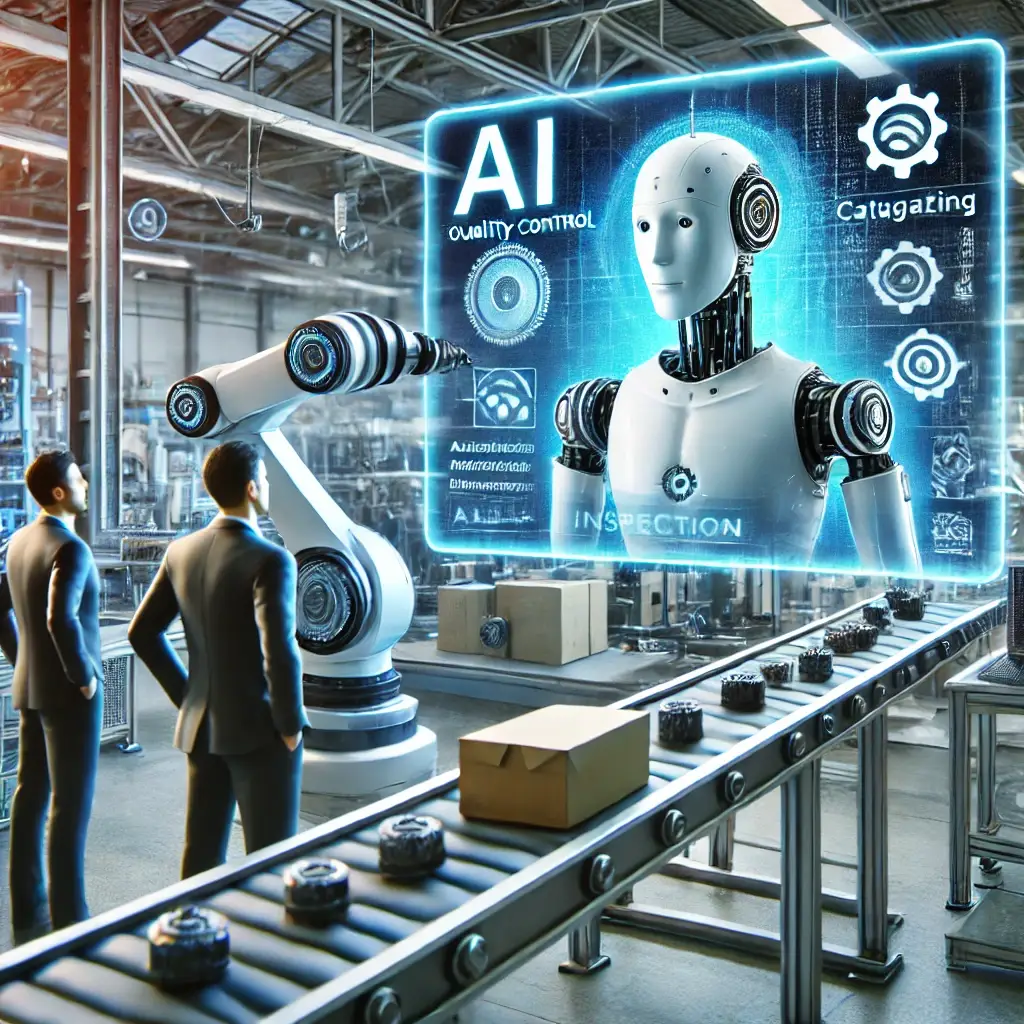
6. π Cybersecurity Challenges in the Evolution of PLCs
With increased IoT integration, PLCs are more vulnerable to cyberattacks. A notable example is the Triton malware attack on industrial control systems in 2017, which specifically targeted safety PLCs, highlighting the growing cybersecurity risks in industrial automation. Such incidents emphasize the need for robust security protocols to protect modern smart factories. Industries must implement:
- π Encrypted communication protocols
- π‘οΈ Multi-layer authentication for remote access
- π Regular security updates and patches
- π§ Network segmentation to protect critical systems
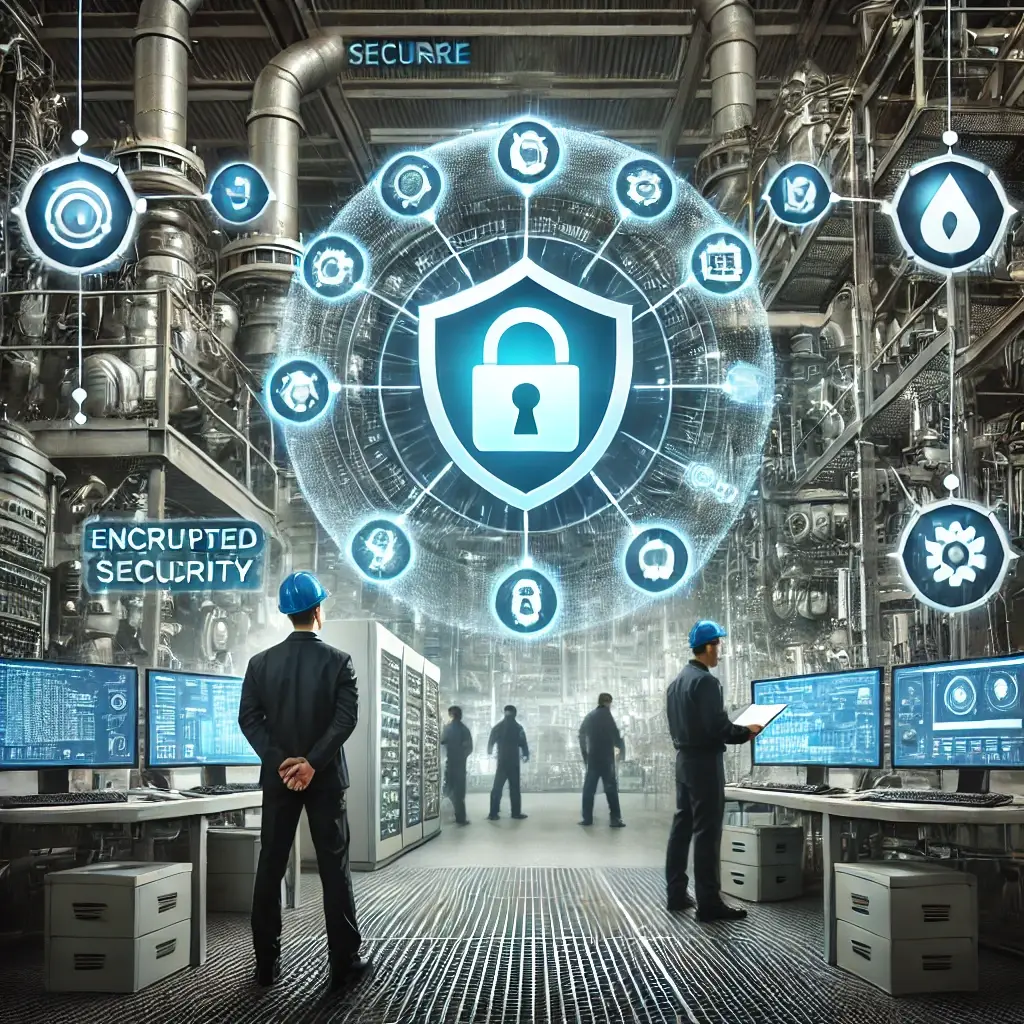
7. π Upgrading Legacy Systems with Modern PLCs
Many factories still operate on decades-old PLCs. Transitioning to modern automation requires careful planning to:
- β Ensure compatibility with existing machinery
- β³ Minimize downtime during upgrades
- ποΈ Train personnel in modern PLC programming
- π οΈ Develop phased migration strategies to avoid disruptions
8. π§ Edge Computing in Industrial Automation
- π Faster real-time data processing for improved efficiency
- π Reduced reliance on cloud computing, ensuring quicker response times
- π Enhanced security by keeping sensitive data local
9. π Digital Twins for Virtual Simulations in PLC Systems
- π οΈ Simulate process changes before implementation
- π Identify potential failures in real-time
- π Optimize production efficiency with AI-driven insights
10. π€ Advanced Robotics & Human-Machine Collaboration with PLCs
- π€ Automated material handling and assembly
- π¦ Collaborative machine tending and packaging
- π― AI-assisted decision-making for workflow optimization
- π· Increased worker safety with predictive risk analysis
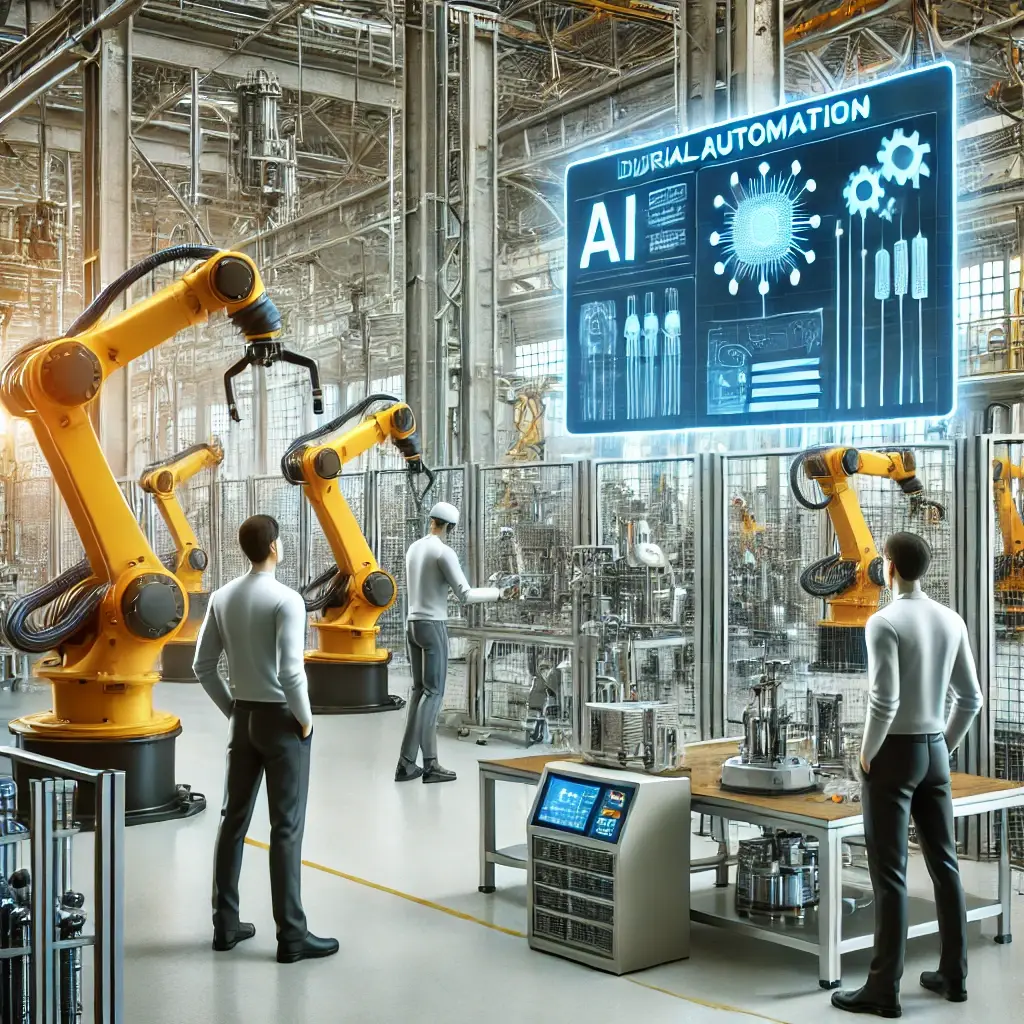
Conclusion
The evolution of Programmable Logic Controllers (PLCs) has played a critical role in industrial automation, enhancing efficiency and innovation. With continuous advancements in IoT integration, cloud-based automation, and machine learning in manufacturing, PLCs are set to define the future of smart factories.
Want to stay updated on the latest trends in industrial automation? Keeping up with industry advancements is essential for engineers and decision-makers looking to improve efficiency, reduce downtime, and stay ahead in an increasingly competitive market. Check out these leading resources:
π Rockwell Automation
π Schneider Electric